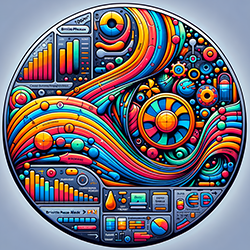
DPM: ANSYS Fluent CFD Simulation Training Course
Price:
$800.00
$349.00
“DPM: All Levels” is a comprehensive course on the Discrete Phase Model (DPM) in ANSYS Fluent, designed for engineers and researchers working with dispersed phase simulations. This course covers DPM fundamentals, software implementation, and practical applications through six detailed chapters. Starting with DPM concepts and Lagrangian framework, the course progresses to explore ANSYS Fluent’s DPM interface, including injection types, particle treatments, and boundary conditions. Participants will master advanced topics such as spraying with evaporation and breakup, wet combustion, erosion modeling, and respiratory disease simulations. Through hands-on examples and in-depth explanations, learners will gain the skills to tackle complex multiphase flow problems across various industries, making this course essential for both newcomers and experienced users seeking to enhance their DPM expertise in CFD simulations.
Wet Combustion by DPM Combusting Particle CFD Simulation
Master Wet Combustion Simulation: Advanced DPM Techniques with Combusting Particles Dive into the complex world of wet combustion modeling in our fourth episode of the “DPM: All Levels” course. This advanced tutorial showcases the power of ANSYS Fluent’s Discrete Phase Model (DPM) in simulating intricate combustion processes, focusing on anthracite volatile combustion in a chamber. Episode Overview In this cutting-edge simulation project, you’ll learn to model the wet combustion of anthracite particles, tracking their journey from devolatilization to oxidation. By combining the Discrete Phase Model (DPM) with Species Transport, you’ll capture the full spectrum of combustion dynamics, including the production of carbon dioxide and water vapor. Key Learning Objectives 1. Advanced Combustion Modeling - Master the simulation of wet combustion using combusting particles in DPM - Implement Species Transport for accurate multi-component reaction modeling - Understand the interplay between particle dynamics and combustion processes 2. Realistic Fuel Particle Simulation - Model anthracite particles with 2% liquid fraction and 0.5-second injection duration - Simulate particle heating, devolatilization, and subsequent oxidation - Incorporate non-spherical particle shapes and Rosin-Rammler diameter distribution 3. Complex Reaction Dynamics - Track the release and oxidation of volatile fractions - Model the production of carbon dioxide and water vapor - Analyze temperature evolution in the combustion chamber (up to 2400K) 4. Advanced Mesh Generation and Optimization - Create geometry using ANSYS Design Modeler - Generate unstructured mesh grids with ANSYS Meshing - Convert to polyhedron cells for reduced computational costs Why This Episode Is Crucial This advanced tutorial provides: Hands-on experience with state-of-the-art combustion simulation techniques Insights into complex multiphase phenomena in real-world combustion applications Skills to model and analyze intricate particle-fluid-reaction interactions Foundation for tackling challenging industrial combustion problems Who Should Watch This episode is ideal for: CFD engineers working on combustion systems and energy conversion processes Researchers in fields such as power generation, industrial furnaces, and emission control ANSYS Fluent users looking to enhance their DPM and combustion modeling capabilities Industry professionals dealing with coal combustion, biomass burning, or waste incineration Elevate Your Combustion Simulation Expertise Don’t miss this opportunity to master advanced wet combustion modeling techniques. Whether you’re optimizing furnace designs, improving combustion efficiency, or developing new clean energy technologies, the skills you’ll gain in this episode are invaluable for accurate and efficient simulations. What You'll Achieve By the end of this episode, you’ll be able to: Set up complex DPM simulations for wet combustion applications Model realistic fuel particle behavior, including devolatilization and oxidation Analyze combustion products and temperature distributions Apply advanced meshing techniques for optimized simulations Visualize and interpret complex combustion dynamics results Prepare for Industry-Leading Combustion Simulations Enroll now to take your DPM and combustion modeling skills to the next level. This episode will empower you to tackle real-world combustion simulation challenges with confidence, opening new possibilities in energy efficiency, emission reduction, and combustion system design. Join us in exploring the cutting edge of multiphase reactive flow modeling!
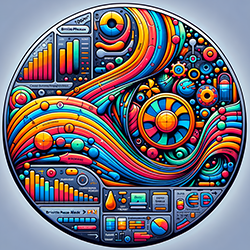
DPM: ANSYS Fluent CFD Simulation Training Course
“DPM: All Levels” is a comprehensive course on the Discrete Phase Model (DPM) in ANSYS Fluent, designed for engineers and researchers working with dispersed phase simulations. This course covers DPM fundamentals, software implementation, and practical applications through six detailed chapters. Starting with DPM concepts and Lagrangian framework, the course progresses to explore ANSYS Fluent’s DPM interface, including injection types, particle treatments, and boundary conditions. Participants will master advanced topics such as spraying with evaporation and breakup, wet combustion, erosion modeling, and respiratory disease simulations. Through hands-on examples and in-depth explanations, learners will gain the skills to tackle complex multiphase flow problems across various industries, making this course essential for both newcomers and experienced users seeking to enhance their DPM expertise in CFD simulations.
Wet Combustion by DPM Combusting Particle CFD Simulation
Master Wet Combustion Simulation: Advanced DPM Techniques with Combusting Particles Dive into the complex world of wet combustion modeling in our fourth episode of the “DPM: All Levels” course. This advanced tutorial showcases the power of ANSYS Fluent’s Discrete Phase Model (DPM) in simulating intricate combustion processes, focusing on anthracite volatile combustion in a chamber. Episode Overview In this cutting-edge simulation project, you’ll learn to model the wet combustion of anthracite particles, tracking their journey from devolatilization to oxidation. By combining the Discrete Phase Model (DPM) with Species Transport, you’ll capture the full spectrum of combustion dynamics, including the production of carbon dioxide and water vapor. Key Learning Objectives 1. Advanced Combustion Modeling - Master the simulation of wet combustion using combusting particles in DPM - Implement Species Transport for accurate multi-component reaction modeling - Understand the interplay between particle dynamics and combustion processes 2. Realistic Fuel Particle Simulation - Model anthracite particles with 2% liquid fraction and 0.5-second injection duration - Simulate particle heating, devolatilization, and subsequent oxidation - Incorporate non-spherical particle shapes and Rosin-Rammler diameter distribution 3. Complex Reaction Dynamics - Track the release and oxidation of volatile fractions - Model the production of carbon dioxide and water vapor - Analyze temperature evolution in the combustion chamber (up to 2400K) 4. Advanced Mesh Generation and Optimization - Create geometry using ANSYS Design Modeler - Generate unstructured mesh grids with ANSYS Meshing - Convert to polyhedron cells for reduced computational costs Why This Episode Is Crucial This advanced tutorial provides: Hands-on experience with state-of-the-art combustion simulation techniques Insights into complex multiphase phenomena in real-world combustion applications Skills to model and analyze intricate particle-fluid-reaction interactions Foundation for tackling challenging industrial combustion problems Who Should Watch This episode is ideal for: CFD engineers working on combustion systems and energy conversion processes Researchers in fields such as power generation, industrial furnaces, and emission control ANSYS Fluent users looking to enhance their DPM and combustion modeling capabilities Industry professionals dealing with coal combustion, biomass burning, or waste incineration Elevate Your Combustion Simulation Expertise Don’t miss this opportunity to master advanced wet combustion modeling techniques. Whether you’re optimizing furnace designs, improving combustion efficiency, or developing new clean energy technologies, the skills you’ll gain in this episode are invaluable for accurate and efficient simulations. What You'll Achieve By the end of this episode, you’ll be able to: Set up complex DPM simulations for wet combustion applications Model realistic fuel particle behavior, including devolatilization and oxidation Analyze combustion products and temperature distributions Apply advanced meshing techniques for optimized simulations Visualize and interpret complex combustion dynamics results Prepare for Industry-Leading Combustion Simulations Enroll now to take your DPM and combustion modeling skills to the next level. This episode will empower you to tackle real-world combustion simulation challenges with confidence, opening new possibilities in energy efficiency, emission reduction, and combustion system design. Join us in exploring the cutting edge of multiphase reactive flow modeling!
-
Section 1
Concept
-
Introduction to Discrete Phase Model (DPM) Concepts: Mastering Multiphase Flow Simulations Embark on your journey to become a Discrete Phase Model (DPM) expert with this foundational episode of our “DPM: All Levels” course. Dive deep into the core concepts that underpin this powerful multiphase flow simulation technique in ANSYS Fluent. Episode Overview This comprehensive introduction sets the stage for your DPM mastery. You’ll gain a solid understanding of the fundamental principles, applications, and considerations essential for successful DPM simulations. Key Learning Objectives 1. DPM Fundamentals - Grasp the essence of Discrete Phase Modeling - Understand the key requirements and assumptions for DPM simulations - Explore the Lagrangian Framework Reference and its significance 2. Real-World Applications - Discover diverse industrial applications of DPM - Analyze real-world examples showcasing DPM's problem-solving capabilities 3. DPM Advantages and Limitations - Compare DPM to other multiphase flow models - Understand when to choose DPM for your simulations - Introduction to Dense Discrete Phase Model (DDPM) for high particle concentrations 4. Particle Dynamics - Explore the concept of Particle Life Cycle - Delve into Governing & Trajectories Equations - Understand Particle Fate and its implications 5. Simulation Best Practices - Learn the importance of grid-independence studies in DPM cases - Gain insights into optimizing your DPM simulations for accuracy and efficiency Why This Episode Is Crucial As the foundation of our DPM course, this episode equips you with the essential knowledge to: Understand when and how to apply DPM in your CFD projects Make informed decisions about simulation parameters Interpret DPM results with confidence Lay the groundwork for advanced DPM techniques covered in later episodes Who Should Watch This episode is perfect for: CFD engineers new to multiphase flow simulations Experienced simulators looking to refresh their DPM knowledge Researchers exploring particle-laden flow phenomena Industry professionals seeking to expand their simulation capabilities Start Your DPM Journey Today Don’t miss this opportunity to build a strong foundation in Discrete Phase Modeling. Whether you’re tackling spray dynamics, particle transport, or erosion simulations, the concepts covered in this episode are your first step towards DPM mastery. What's Next? After completing this introductory episode, you’ll be well-prepared to dive into more advanced DPM topics, including: Detailed ANSYS Fluent DPM interface navigation Complex spray simulations with evaporation and breakup Wet combustion modeling Erosion analysis in channels Respiratory disease transmission simulations Enroll now and take the first step towards becoming a DPM expert. Your journey to mastering multiphase flow simulations starts here!
Episode 1 12m 27s Free Episode
-
-
Section 2
DPM in ANSYS Fluent
-
Mastering the Discrete Phase Model (DPM) in ANSYS FLUENT: A Comprehensive Guide Dive deep into the heart of multiphase flow simulations with our second episode of the “DPM: All Levels” course. This comprehensive tutorial unlocks the full potential of the Discrete Phase Model (DPM) module in ANSYS FLUENT, equipping you with the knowledge to tackle complex particle-laden flow problems with confidence. Episode Overview In this extensive exploration of ANSYS FLUENT’s DPM capabilities, you’ll gain hands-on experience navigating the software’s interface and mastering its diverse features. From basic settings to advanced modeling techniques, this episode covers it all, ensuring you’re well-prepared to implement DPM in your simulations effectively. Key Learning Objectives 1. DPM Dialog Box Mastery - Navigate the Discrete Phase Model Dialog Box with ease - Understand interaction settings and particle treatment options - Master tracking parameters for precise simulations 2. Advanced Physical Models - Explore a wide range of physical phenomena, including: - Particle Radiation Interaction - Thermophoretic and Saffman Lift forces - Virtual mass and Pressure gradient forces - Erosion/Accretion modeling - Temperature-dependent effects - Two-way turbulence coupling - Collision and breakup models 3. Injection Techniques - Learn various injection types: Single, Group, Surface, and Cone - Understand different particle types: Massless, Inert, Droplet, Combusting, and Multi-component - Master diameter distribution methods for realistic particle populations 4. Drag Laws and Breakup Models - Implement appropriate drag laws for your specific applications - Understand and apply breakup models for complex multiphase flows 5. Turbulent Dispersion and Boundary Conditions - Grasp the concepts of Stochastic tracking and Cloud tracking - Master DPM boundary conditions for accurate particle-wall interactions Why This Episode Is Essential As the cornerstone of our DPM course, this episode provides: In-depth understanding of ANSYS FLUENT’s DPM interface Practical skills to set up and customize DPM simulations Knowledge to choose appropriate models for your specific engineering problems Foundation for advanced DPM applications covered in later episodes Who Should Watch This episode is invaluable for: CFD engineers looking to expand their multiphase modeling capabilities Researchers working on particle-laden flows in various industries ANSYS FLUENT users aiming to leverage DPM for complex simulations Students and professionals seeking to enhance their CFD skillset Elevate Your DPM Expertise with ANSYS FLUENT Don’t miss this opportunity to become proficient in one of the most powerful tools for multiphase flow simulations. Whether you’re simulating sprays, particle transport, or erosion phenomena, the skills you’ll gain in this episode are essential for accurate and efficient DPM modeling. What's Next? After mastering the ANSYS FLUENT DPM interface, you’ll be well-prepared to tackle the practical applications covered in subsequent episodes, including: Spray simulations with evaporation and breakup Wet combustion modeling Erosion analysis in complex geometries Respiratory disease transmission studies Enroll now and take a significant step towards becoming a DPM expert. Transform your approach to multiphase flow simulations and unlock new possibilities in your engineering and research projects!
Episode 1 47m 9s
-
-
Section 3
Spray (Breakup and Evaporation)
-
Master Advanced Water Spraying Simulation: Breakup and Evaporation Using DPM in ANSYS Fluent Dive into the complexities of water spraying dynamics with our third episode of the “DPM: All Levels” course. This comprehensive tutorial showcases the power of the Discrete Phase Model (DPM) in simulating intricate spray behaviors, including droplet breakup and evaporation. Episode Overview In this cutting-edge simulation project, you’ll learn to model water spraying from a nozzle with unprecedented accuracy. By combining the Discrete Phase Model (DPM) with the Species Transport model, you’ll capture the full spectrum of spray dynamics, from droplet formation to evaporation and film formation. Key Learning Objectives 1. Advanced DPM Techniques - Master the simulation of water spraying considering droplet breakup and evaporation - Implement the Species Transport model for accurate phase change modeling - Understand the interplay between particle dynamics and environmental conditions 2. Realistic Spray Modeling - Simulate 2 mm diameter water droplets injected at 1.25 m/s - Model evaporation triggers at specific temperature thresholds (282.5K) - Incorporate stochastic collision, coalescence, and droplet breakup using the Taylor Analogy Breakup (TAB) model 3. Complex Particle Dynamics - Apply dynamic-drag law for non-spherical droplet shapes - Utilize the Discrete Random Walk Model for turbulent dispersion - Implement Wall-film DPM boundary conditions for realistic surface interactions 4. Results Analysis and Visualization - Interpret diameter distribution contours ranging from 0.002mm to 7mm - Analyze droplet behavior upon surface impact (sticking, rebounding, spreading, splashing) - Visualize spray dynamics through animations and contour plots Why This Episode Is Crucial This advanced tutorial provides: Hands-on experience with state-of-the-art spray simulation techniques Insights into complex multiphase phenomena in real-world applications Skills to model and analyze intricate particle-fluid interactions Foundation for tackling challenging industrial spray problems Who Should Watch This episode is ideal for: CFD engineers working on spray systems and atomization processes Researchers in fields such as automotive, aerospace, and chemical engineering ANSYS Fluent users looking to enhance their DPM simulation capabilities Industry professionals dealing with spray cooling, fuel injection, or coating processes Elevate Your Spray Simulation Expertise Don’t miss this opportunity to master advanced spray modeling techniques. Whether you’re optimizing nozzle designs, improving combustion processes, or developing new spray technologies, the skills you’ll gain in this episode are invaluable for accurate and efficient simulations. What You'll Achieve By the end of this episode, you’ll be able to: Set up complex DPM simulations for spray applications Model realistic droplet behavior, including breakup and evaporation Analyze spray patterns and droplet size distributions Apply advanced boundary conditions for surface interactions Visualize and interpret complex spray dynamics results Prepare for Industry-Leading Simulations Enroll now to take your DPM skills to the next level. This episode will empower you to tackle real-world spray simulation challenges with confidence, opening new possibilities in product design, process optimization, and research applications. Join us in exploring the cutting edge of multiphase flow modeling!
Episode 1 30m 53s
-
-
Section 4
Respiratory Disease Transmission
-
Optimize ICU Ventilation Design: Preventing Respiratory Disease Transmission & Enhancing Thermal Comfort Embark on a critical journey of healthcare facility optimization in our sixth episode of the “DPM: All Levels” course. This advanced tutorial demonstrates the power of ANSYS Fluent’s Discrete Phase Model (DPM) in simulating and improving Intensive Care Unit (ICU) ventilation systems, focusing on both disease prevention and patient comfort. Episode Overview In this cutting-edge simulation project, you’ll learn to model and optimize ICU ventilation systems, balancing the crucial needs of preventing respiratory disease transmission and maintaining optimal thermal comfort. By leveraging DPM with advanced HVAC modeling techniques, you’ll gain invaluable skills in healthcare facility design and improvement. Key Learning Objectives 1. Advanced ICU Ventilation Modeling - Master the simulation of airflow patterns and particle dispersion in healthcare settings - Implement thermal comfort models (PMV & PPD) for patient and staff well-being - Understand the critical balance between disease prevention and comfort in ICU design 2. Respiratory Disease Transmission Simulation - Model the dispersion of virus-laden aerosols from infected patients - Analyze particle residence time and its impact on infection risk - Optimize ventilation strategies to minimize disease transmission 3. Thermal Comfort Optimization - Visualize and interpret Predicted Mean Vote (PMV) and Percentage People Dissatisfied (PPD) indices - Analyze the impact of various HVAC configurations on thermal comfort - Optimize inlet and outlet placements for ideal comfort conditions 4. Iterative Design Improvement - Evaluate three distinct ICU ventilation designs: 1. Conventional opposite wall inlet/outlet system 2. Cross-ventilation with strategically placed outlets 3. Optimized ceiling inlet with patient-specific outlets - Analyze the pros and cons of each design iteration Why This Episode Is Crucial This advanced tutorial provides: Hands-on experience with state-of-the-art healthcare facility simulation techniques Insights into the complex interplay between airflow, disease transmission, and thermal comfort Skills to model and analyze critical healthcare environments Foundation for tackling real-world healthcare design challenges Who Should Watch This episode is ideal for: CFD engineers working on healthcare facility design and optimization HVAC specialists focusing on critical care environments Researchers in fields such as indoor air quality, infection control, and hospital design Healthcare facility managers and designers seeking to improve patient and staff safety Elevate Your Healthcare Facility Design Expertise Don’t miss this opportunity to master advanced ICU ventilation modeling techniques. Whether you’re designing new healthcare facilities, retrofitting existing ones, or developing innovative infection control strategies, the skills you’ll gain in this episode are invaluable for creating safer and more comfortable healthcare environments. What You'll Achieve By the end of this episode, you’ll be able to: Set up complex DPM simulations for healthcare ventilation applications Model and analyze respiratory disease transmission risks in ICU settings Optimize HVAC systems for both infection control and thermal comfort Apply iterative design processes to achieve optimal ICU environments Visualize and interpret complex airflow and comfort data for healthcare decision-making Prepare for Industry-Leading Healthcare Facility Simulations Enroll now to take your healthcare facility modeling skills to the next level. This episode will empower you to tackle real-world ICU design challenges with confidence, opening new possibilities in patient safety, staff comfort, and overall healthcare efficiency. Join us in exploring the cutting edge of healthcare environment modeling and optimization!
Episode 1 31m 42s
-
-
Section 5
Erosion
-
Master Erosion Simulation in Complex Geometries: Advanced DPM Techniques for Obstruction Channels Dive into the intricate world of erosion modeling in our fifth episode of the “DPM: All Levels” course. This advanced tutorial showcases the power of ANSYS Fluent’s Discrete Phase Model (DPM) in simulating erosion phenomena in an obstruction channel, providing crucial insights for industrial applications. Episode Overview In this cutting-edge simulation project, you’ll learn to model the flow of impure water through an obstruction channel, focusing on the impact of sand particles on erosion patterns. By leveraging the Discrete Phase Model (DPM) with erosion/accretion modeling, you’ll gain valuable skills in predicting and analyzing long-term wear in complex flow systems. Key Learning Objectives 1. Advanced Erosion Modeling - Master the simulation of particle-induced erosion using DPM - Implement two-way coupling for accurate particle-fluid interactions - Understand the impact of obstacles on flow patterns and erosion rates 2. Realistic Particle Simulation - Model 1mm diameter sand particles in high-velocity water flow - Simulate particle trajectories and their impact on channel surfaces - Analyze residence time and its relation to erosion patterns 3. Complex Flow Dynamics - Visualize and interpret velocity and pressure gradients in obstructed channels - Understand the formation of high-velocity regions (up to 93.5 m/s) - Analyze the influence of channel geometry on erosion hotspots 4. Advanced Mesh Generation and Solver Settings - Create detailed geometry using ANSYS Design Modeler - Generate structured mesh grids with over 1 million quad elements - Configure steady-state solver settings for erosion/accretion phenomena Why This Episode Is Crucial This advanced tutorial provides: Hands-on experience with state-of-the-art erosion simulation techniques Insights into complex multiphase phenomena in industrial flow systems Skills to model and analyze long-term wear in obstructed channels Foundation for tackling challenging erosion problems in various industries Who Should Watch This episode is ideal for: CFD engineers working on pipeline systems, hydraulic machinery, or sediment transport Researchers in fields such as oil and gas, water treatment, and mineral processing ANSYS Fluent users looking to enhance their DPM and erosion modeling capabilities Industry professionals dealing with wear prediction, maintenance planning, or design optimization Elevate Your Erosion Simulation Expertise Don’t miss this opportunity to master advanced erosion modeling techniques. Whether you’re optimizing pipeline designs, improving wear resistance in hydraulic systems, or developing new erosion mitigation strategies, the skills you’ll gain in this episode are invaluable for accurate and efficient simulations. What You'll Achieve By the end of this episode, you’ll be able to: Set up complex DPM simulations for erosion applications in obstructed channels Model realistic particle behavior and its impact on surface wear Analyze flow patterns and their correlation with erosion hotspots Apply various erosion theories (Oka, Mclaury, Finnie) for comprehensive analysis Visualize and interpret complex erosion dynamics results Prepare for Industry-Leading Erosion Simulations Enroll now to take your DPM and erosion modeling skills to the next level. This episode will empower you to tackle real-world erosion simulation challenges with confidence, opening new possibilities in equipment longevity, maintenance scheduling, and system design optimization. Join us in exploring the cutting edge of multiphase flow and wear prediction modeling!
Episode 1 17m 47s
-
-
Section 6
Combusting Particle (Wet Combustion)
-
Master Wet Combustion Simulation: Advanced DPM Techniques with Combusting Particles Dive into the complex world of wet combustion modeling in our fourth episode of the “DPM: All Levels” course. This advanced tutorial showcases the power of ANSYS Fluent’s Discrete Phase Model (DPM) in simulating intricate combustion processes, focusing on anthracite volatile combustion in a chamber. Episode Overview In this cutting-edge simulation project, you’ll learn to model the wet combustion of anthracite particles, tracking their journey from devolatilization to oxidation. By combining the Discrete Phase Model (DPM) with Species Transport, you’ll capture the full spectrum of combustion dynamics, including the production of carbon dioxide and water vapor. Key Learning Objectives 1. Advanced Combustion Modeling - Master the simulation of wet combustion using combusting particles in DPM - Implement Species Transport for accurate multi-component reaction modeling - Understand the interplay between particle dynamics and combustion processes 2. Realistic Fuel Particle Simulation - Model anthracite particles with 2% liquid fraction and 0.5-second injection duration - Simulate particle heating, devolatilization, and subsequent oxidation - Incorporate non-spherical particle shapes and Rosin-Rammler diameter distribution 3. Complex Reaction Dynamics - Track the release and oxidation of volatile fractions - Model the production of carbon dioxide and water vapor - Analyze temperature evolution in the combustion chamber (up to 2400K) 4. Advanced Mesh Generation and Optimization - Create geometry using ANSYS Design Modeler - Generate unstructured mesh grids with ANSYS Meshing - Convert to polyhedron cells for reduced computational costs Why This Episode Is Crucial This advanced tutorial provides: Hands-on experience with state-of-the-art combustion simulation techniques Insights into complex multiphase phenomena in real-world combustion applications Skills to model and analyze intricate particle-fluid-reaction interactions Foundation for tackling challenging industrial combustion problems Who Should Watch This episode is ideal for: CFD engineers working on combustion systems and energy conversion processes Researchers in fields such as power generation, industrial furnaces, and emission control ANSYS Fluent users looking to enhance their DPM and combustion modeling capabilities Industry professionals dealing with coal combustion, biomass burning, or waste incineration Elevate Your Combustion Simulation Expertise Don’t miss this opportunity to master advanced wet combustion modeling techniques. Whether you’re optimizing furnace designs, improving combustion efficiency, or developing new clean energy technologies, the skills you’ll gain in this episode are invaluable for accurate and efficient simulations. What You'll Achieve By the end of this episode, you’ll be able to: Set up complex DPM simulations for wet combustion applications Model realistic fuel particle behavior, including devolatilization and oxidation Analyze combustion products and temperature distributions Apply advanced meshing techniques for optimized simulations Visualize and interpret complex combustion dynamics results Prepare for Industry-Leading Combustion Simulations Enroll now to take your DPM and combustion modeling skills to the next level. This episode will empower you to tackle real-world combustion simulation challenges with confidence, opening new possibilities in energy efficiency, emission reduction, and combustion system design. Join us in exploring the cutting edge of multiphase reactive flow modeling!
Episode 1 29m 50s
-
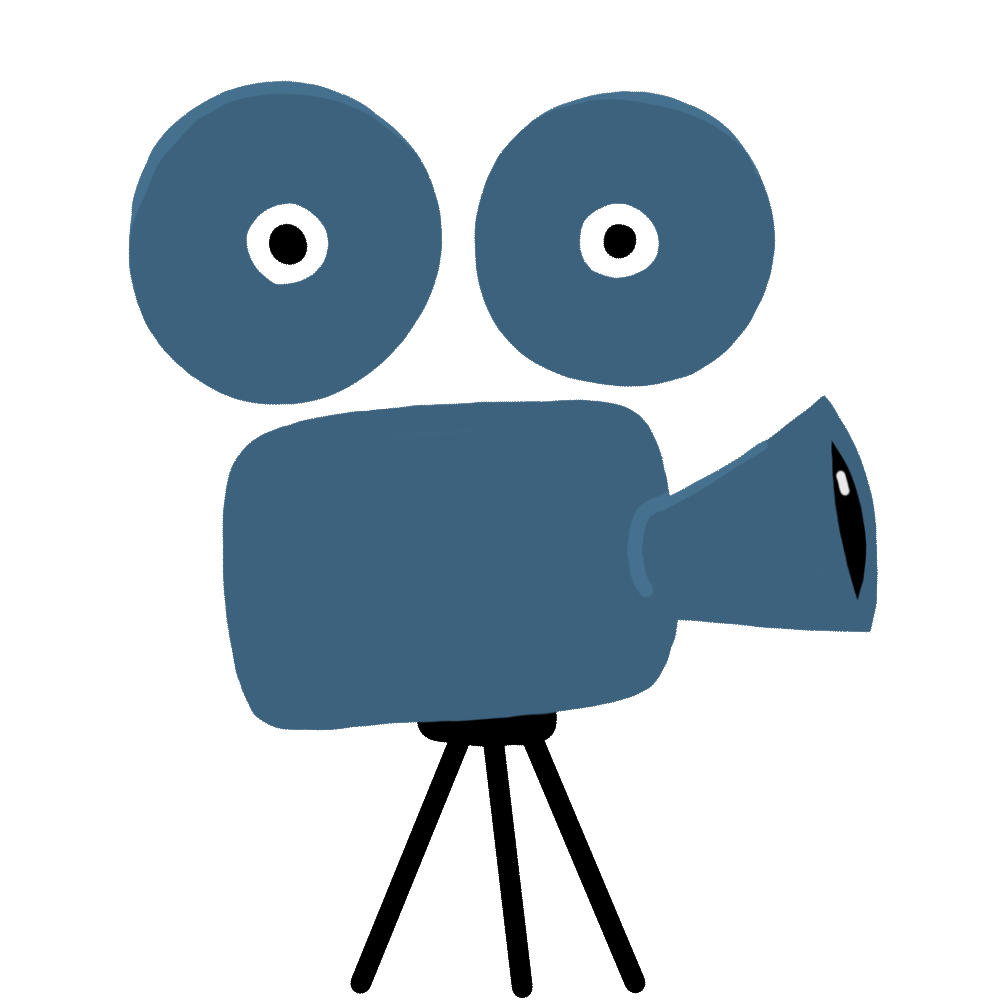
Course In Progress
Course still in development. Check back often for updates.
Master the Discrete Phase Model (DPM) in ANSYS Fluent: From Fundamentals to Advanced Applications
Unlock the power of multiphase flow simulations with our comprehensive “DPM: All Levels” course. Designed for engineers, researchers, and CFD enthusiasts, this in-depth training will equip you with the skills to tackle complex dispersed phase problems using ANSYS Fluent’s Discrete Phase Model (DPM).
Course Overview
Our expertly crafted curriculum takes you on a journey from DPM basics to advanced applications, ensuring you gain both theoretical knowledge and practical skills. Through six detailed chapters, you’ll master the intricacies of DPM simulations, enabling you to solve real-world engineering challenges across various industries.
What You'll Learn
1. DPM Fundamentals
- Grasp the core concepts of the Discrete Phase Model - Understand Lagrangian Framework Reference - Explore DPM applications in industry - Analyze DPM advantages, limitations, and comparisons with other models
2. ANSYS Fluent DPM Interface
- Navigate the Discrete Phase Model Dialog Box - Master injection types, particle treatments, and tracking parameters - Explore physical models including particle radiation interaction and force models - Understand breakup models, turbulent dispersion, and DPM boundary conditions
3. Advanced DPM Applications
- Simulate water spraying with evaporation and droplet breakup - Model wet combustion of anthracite volatile - Analyze erosion in obstruction channels - Design ICU environments considering disease transmission
Course Structure
Our course is divided into six comprehensive chapters:
- DPM Concepts
- Exploring ANSYS Fluent DPM Interface
- Spraying Simulation
- Wet Combustion Modeling
- Erosion in Channels
- Respiratory Disease Simulation
Each chapter combines theoretical explanations with hands-on exercises, ensuring you gain practical experience alongside conceptual understanding.
Who Should Enroll?
This course is perfect for:
- CFD engineers looking to expand their multiphase flow modeling skills
- Researchers in fields such as chemical, mechanical, and environmental engineering
- Industry professionals dealing with particle-laden flows, sprays, or erosion problems
- Graduate students focusing on computational fluid dynamics
Why Choose Our DPM Course?
- Comprehensive coverage from basics to advanced topics
- Hands-on experience with real-world engineering problems
- Expert instruction on ANSYS Fluent’s DPM module
- Practical tips and tricks for efficient simulations
- Applicable skills for various industries and research fields
Elevate Your CFD Skills with DPM Mastery
Don’t miss this opportunity to become a DPM expert. Whether you’re new to multiphase flow simulations or looking to refine your skills, our “DPM: All Levels” course provides the knowledge and practical experience you need to excel in your field.
Enroll Now and Unlock the Power of DPM!
Join our course today and transform your approach to multiphase flow simulations. Gain the skills to tackle complex engineering problems, optimize designs, and drive innovation in your industry. Your journey to becoming a DPM expert starts here!
Buy Course
Benefits of buying the whole course
- Complete access to chapters Without Price
- Special discount
- Unlimited access to course content
- Free access to all new and updated content
- Access to course forever without any additional payment
* You can select chapters seperately, but you won't benefit from the list above.
* The items that do not have a price cannot be bought separately and are only available when you buy the whole course.
Congratulations
Congratulations! Your purchase was successful.
You can now start learning the course by clicking the button "Start Learning".
Add Payment Method
Please enter your payment method details.